Understanding Cummins Parts Order for Enhanced Business Efficiency
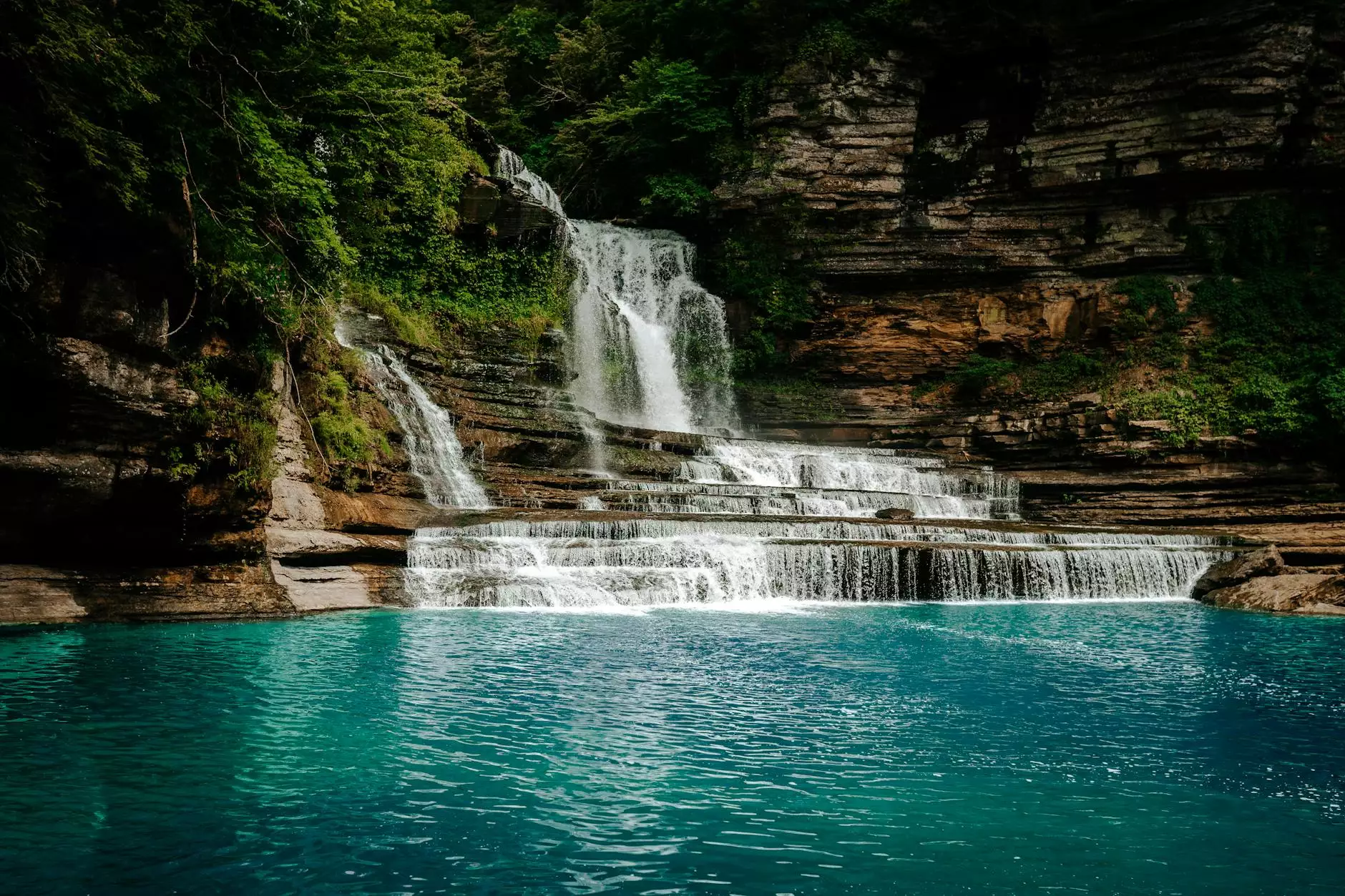
In the competitive world of diesel engine manufacturing and generator supply, having access to high-quality parts is essential for maintaining efficiency and reliability. A well-structured Cummins parts order can significantly impact your operations, ensuring that your equipment runs smoothly and effectively. This article explores the benefits, process, and key considerations involved in ordering Cummins parts to help your business thrive.
Why Choose Cummins Parts?
When it comes to diesel engines, few brands stand out as much as Cummins. Known for their durability and performance, Cummins engines and components are widely sought after in various industries. Here’s why ordering Cummins parts is a strategic choice:
- Quality Assurance: Cummins parts are designed with precision and undergo stringent quality checks, ensuring reliability and longevity.
- Performance Optimization: Genuine Cummins components are engineered to work seamlessly within their engine systems, maximizing efficiency and power.
- Comprehensive Support: When you order Cummins parts, you gain access to a wealth of resources, including technical support, installation guides, and expert advice.
- Warranty Benefits: Using genuine parts not only enhances performance but also keeps your warranty intact, protecting your investment.
The Importance of a Reliable Parts Ordering Process
A reliable Cummins parts order process can streamline your operations, reduce downtime, and ultimately save costs. Here are some critical aspects of an effective ordering system:
1. Accurate Inventory Management
Keeping track of your inventory levels is crucial. Utilizing inventory management systems can help maintain transparency and predict when parts will need replenishing. Regular assessment of stock levels prevents unexpected outages that can halt operations.
2. Established Supplier Relations
Building strong relationships with authorized Cummins dealers ensures you have a trusted source for parts. Reliable suppliers can offer insights into the best-performing components and advise on the latest products available.
3. Efficient Order Placement
Having a streamlined order placement process saves time and reduces errors. This can involve using online platforms or dedicated order management systems to facilitate quick and easy transactions.
4. Timely Delivery
Understanding lead times and establishing clear communication with your supplier ensures that you receive your orders promptly, enabling you to maintain operational continuity.
Navigating the Cummins Parts Order System
The process for placing a Cummins parts order may vary depending on the supplier. However, there are general steps you can follow to simplify the experience:
Step 1: Identify Required Parts
Before placing an order, conduct a thorough assessment of your machinery to determine which parts need replacement or are required for maintenance. Utilizing the Cummins parts catalog can help pinpoint the exact components needed.
Step 2: Gather Necessary Information
Ensure you have all necessary information at hand, including part numbers, descriptions, and your company’s purchasing account details if applicable. This will expedite the ordering process.
Step 3: Place the Order
You can place your order through various channels, including:
- Online Portals: Most suppliers provide user-friendly online interfaces for placing orders quickly and efficiently.
- Phone Orders: Speaking directly with a sales representative can help clarify any questions and ensure accurate orders.
- Email Orders: For larger businesses, sending a detailed email with all necessary specifications can also be effective.
Best Practices for Managing Cummins Parts Orders
To ensure that your parts ordering experience is as seamless as possible, consider these best practices:
1. Maintain a Parts Database
Create a database or spreadsheet that tracks your parts usage, supplier contacts, order history, and replacement schedules. This practice can foster better decision-making and inventory management.
2. Review Supplier Performance
Periodically evaluate your suppliers based on delivery times, parts availability, and customer service quality. This helps in maintaining a relationship with suppliers who contribute positively to your operations.
3. Stay Informed on New Products
Regularly check for updates in Cummins’ product lines. New parts and technologies can provide enhancements in efficiency or performance that can benefit your operations.
4. Leverage Technology
Utilizing ERP (Enterprise Resource Planning) systems can integrate inventory management with your financials, providing a holistic view of your resource allocation and order history.
Common Challenges in Ordering Cummins Parts
While ordering Cummins parts is generally straightforward, you may encounter some challenges:
1. Availability Issues
High demand for specific parts may lead to backorders. Staying proactive in your inventory management can help mitigate this risk.
2. Part Compatibility
Not all parts are compatible with every engine model. Ensure that you verify part numbers against your machinery to prevent issues with assembly.
3. Miscommunication with Suppliers
Clear communication is key to successful orders. Always confirm orders verbally and via email to avoid misunderstandings.
The Future of Cummins Parts Ordering
As technology advances, the future of Cummins parts ordering looks promising. Automation, artificial intelligence, and enhanced data analytics are expected to revolutionize the industry:
1. Predictive Ordering
With advanced analytics, businesses can predict when they will require parts based on past usage trends, automating the re-ordering process.
2. Enhanced Online Platforms
The evolution of online platforms will likely continue, allowing for real-time inventory monitoring, easier part identification, and swift order placements.
3. Improved Logistics Solutions
Investment in logistics technologies will streamline the delivery process, ensuring that parts arrive just-in-time for maintenance and repairs.
Conclusion
Ordering Cummins parts is an essential function for organizations within the diesel engine manufacturing and generator supply sectors. By developing a deep understanding of the parts ordering process and implementing best practices, businesses can enhance operational efficiency and reliability. As technologies continue to evolve, staying innovative and proactive in your parts ordering strategy will keep you ahead in the competitive landscape. Investing time and resources into understanding your Cummins parts orders can yield significant returns, improving your overall business performance.